Returnable packaging and reusable packaging is a cost-effective and environmentally friendly alternative for organizations that have an extensive flow of goods with a limited number of distribution points. It tells customers how responsible your company is, that not only cares about product protection but also about the environment.
The Challenge
Managing a fleet of returnable packaging, like metal pallets is harder than it seems. A closed-loop process for returnable packaging is an important component in managing packaging systems. Metal pallets are routinely misdirected or lost, and they are rarely tracked in ERP systems. Yet it is so critical to control such a large and constantly moving investment, to make it match with supply and demand.
Expendable packaging like wooden pallets are not intended at saving money or the environment. The long-term benefits of using durable materials for returnable packaging like metal pallets far outweigh the expendable packaging thought process. The failure to collect the empties and get them into a condition for reuse is the primary reason why reusable packaging tends to increase total costs. It is for this reason that the processes to manage the returnable packaging will look for the overall, lowest system cost.
Supply Chain
Most firms that choose to invest in their own returnable packaging system (metal pallets or plastic packaging) base their decision on some kind of a supply chain. They usually compare the costs associated with returnable packaging to the expenses for their existing expendable packaging. A decision on a good supply chain model is important as once the product has arrived at the final destination, these pallets must be collected and sent back to the distribution point.
At this time it’s not on the transportation costs that need to be considered but also the loss in transit that need to be considered. Tracking systems for such a supply chain needs to have real-time pallet counts from every point along the channel–every staging, replenishment, and cleaning location–not just shipping and receiving docks. This requires accurate counting, reporting, and sharing application systems.
Pilferage – IoT can help, but which one?
The last few years have seen various technologies that have been deployed to gain visibility of each returnable package through its entire logistics system as it is shipped from its warehouse to its final destination.
I am often asked about what Internet of Things (IoT) technology should be used to help control the costs related to the theft of returnable packagings like iron and plastic pallets. I have tried to explain the advantages and disadvantages of using Barcodes or RFID or NFC or BLE Beacons
1] Barcode technology
In the last decade, we saw digital systems evolve and manual labels on packages got evolved into “Barcodes” which were easily readable using optical scanners. For the first time, supply chain managers were able to scan packages at any hub-points during transit and transmit the data to a central repository or an ERP.
Disadvantages of using Barcodes:
- Time Intensive & Laborious: It takes time of up to 3 seconds to scan a package and if you are looking at shipping multiple packages you could be spending hours and hours to get the job done.
- Inability to provide real-time location: When the returnable packaging is in transit and especially when it’s empty, there is a good chance of pilferage. Here the Barcodes as a solution falls short of expectations.
2] Radio Frequency Identification (RFID) technology
Passive RFID tags (no power from batteries) receive power from the radio signals transmitted by the RFID reader and reflect them back to the readers. While reflecting back, the RFID transmits the data and the reader identifies the data in the tag. In the process of reflecting the radio waves back to the reader, the signal strength weakens and as a result, the range of Passive RFID tags is generally less than 25 feet.
Drawbacks of RFID:
- Short Range: Due to its short read range, the supply chain manager would need to walk the entire floor to cover all corners with a mobile RFID reader. You would need to use quite a few ‘fixed readers’ to cover your entire storage area, and of course incur high maintenance and service costs.
- Complicated Setup: Since passive RFID tags need a reader to communicate and cannot be read using a mobile phone, setup costs and network connectivity can be complex to set up and maintain. For example, setting up a fixed reader in a truck is a very complicated process.
- Cannot provide real-time location: Generally RFID readers do not come equipped with GSM and GPS chips and thus cannot provide real-time location
3] Near-Field Communication (NFC)
Near-Field Communication is a relatively new technology. It is very similar to RFID as it operates at the same bandwidth. Just like RFID, the NFC reader can send a small surge of power to the NFC tag and the tag can reflect the signal back with the data it holds. Some NFC tags may also have a small battery that can send a signal to the NFC reader.
As most mobile phones are now equipped with NFC, the dependency on special readers is not there. But, as this technology has a read range of only a few centimeters, it cannot be used in the logistics system.
4] Bluetooth Low Energy (BLE) Beacons
BLE Beacons with Bluetooth 5.0 protocol are highly energy efficient. A small battery attached to the beacon can last up to 5 years, making them completely maintenance-free. This and its ability to communicate over long ranges is I would say the biggest difference between BLE and RFID. BLE Beacons also have a strategic advantage in terms of cost-effectiveness and scalability.
Advantages of using BLE Beacons for returnable packaging
- Beacons can be read using a cellphone so you do not need network creation, router installations, or WiFi zones.
- Real-time location: by A BLE Gateway (reader for BLE beacons) is generally equipped with Wi-Fi / GSM and GPS and can easily track the location of the truck in transit including the returnable package inside the truck
- Large Transmission power: Beacons have a high transmission power and can send data up to 100 meters for any reader in sight.
- Cost-Effective: Bluetooth protocol and effective power management make deploying Bluetooth beacons very cost-effective. This strategy is by far the most effective one in packaging solutions.
In Summary
YES, the Internet of Things (IoT) can handle returnable packaging by effectively locating the whereabouts of the protective packaging. I would thus like to say that returnable packaging is a great option for many businesses due to the environmental, product safety, and cost benefits that these solutions provide, but they aren’t right for every business. That’s why it is so important to have an experienced IoT provider on your side to help create the best packaging option for your business.
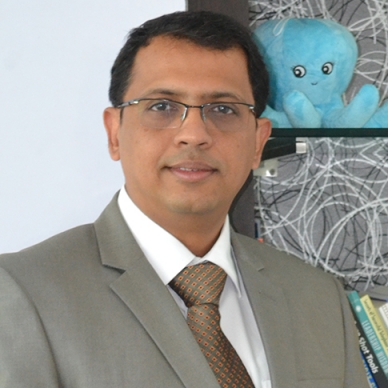